Case study
Vertical Aerospace
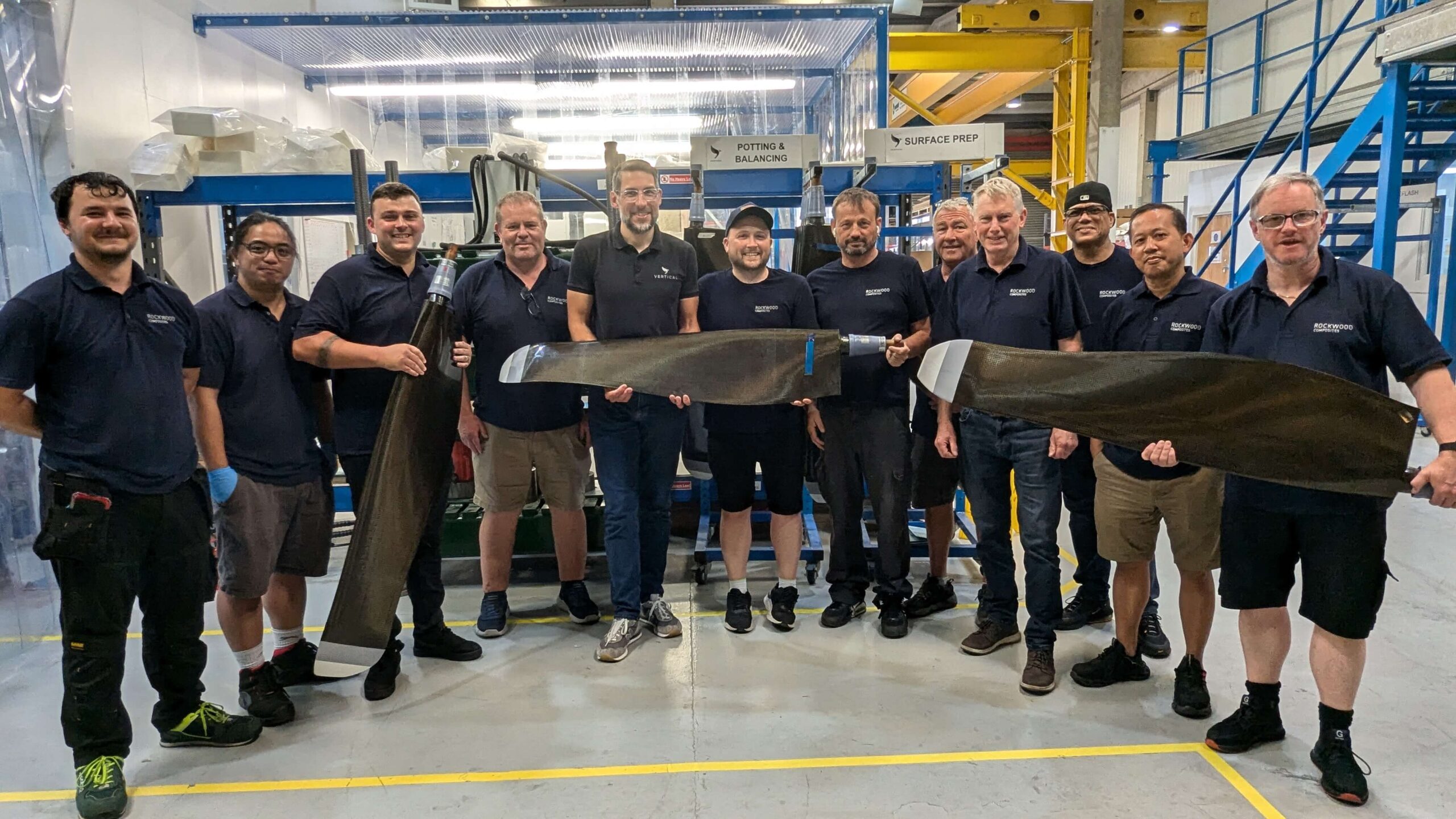
Challenge Overview
Vertical Aerospace sought to develop an improved manufacturing procedure for their Gen 2 forward propellor blade that eliminated the need for secondary bonding operations. The goal was to supply test blades and ultimately flight-certified blades for two prototype aircraft. Previously, the Gen 1 blade was developed as two separate mouldings—the spar and aerofoil shell—which were then bonded together, raising concerns about bond line integrity.
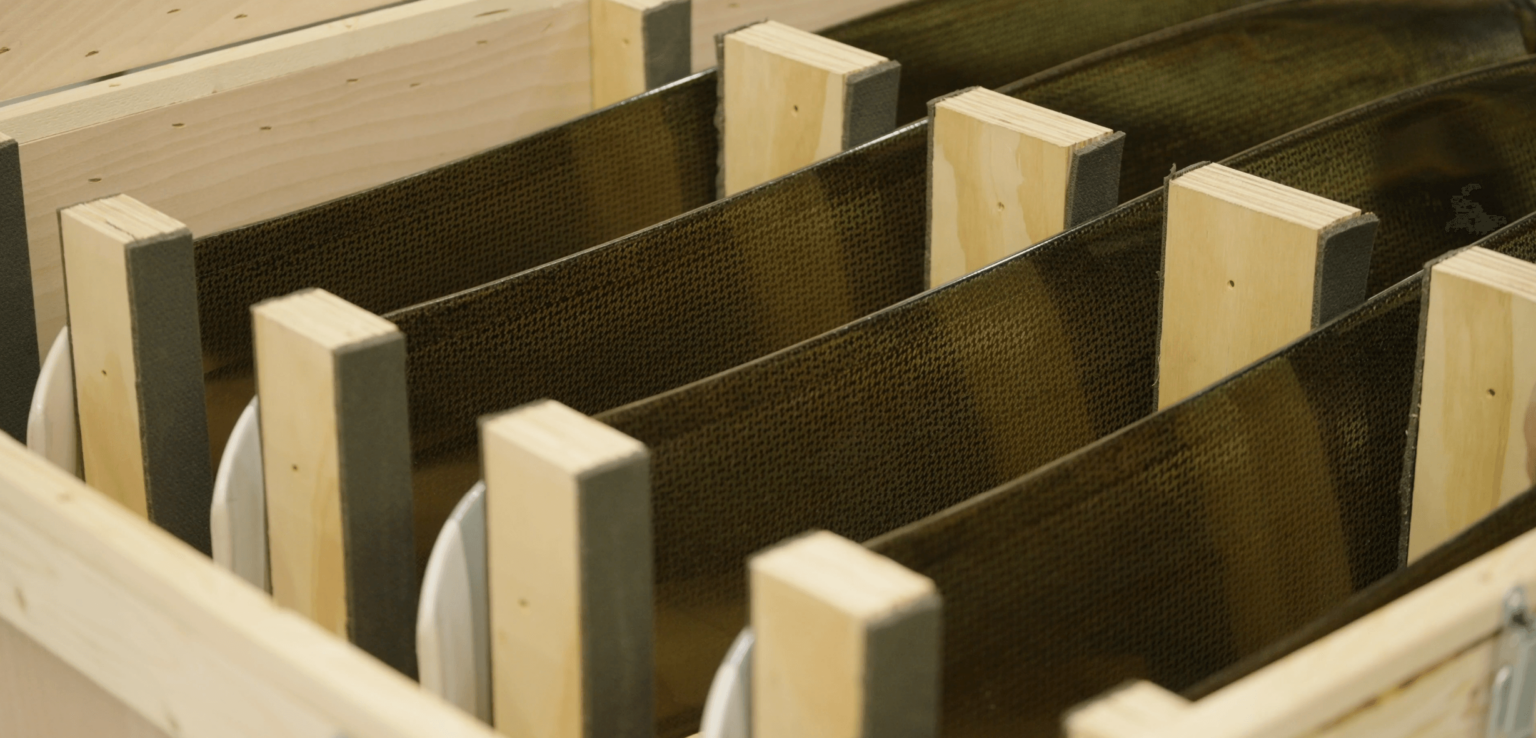
The Solution
Rockwood Aerospace, a division of The Rockwood Group renowned for their expertise in compression moulding, introduced cutting-edge technology to address this challenge. Their innovative one-shot curing technique eliminated secondary bonding operations, producing fully finished blades in a single manufacturing step.
Using an in-house designed aluminium mould tool with side and end action tooling inserts, Rockwood consolidated the moulding within a hot platen press. They developed Rohacell Hero Foam cores to ensure optimal consolidation pressure on the pre-preg materials during curing. These cores were CNC machined with high accuracy and fully laser inspected before laminating to ensure quality assurance.
Given that pre-preg materials and their epoxy resin systems alone were insufficient as the primary adhesive method between the pre-preg skin and porous foam cores, Rockwood used film adhesive to ensure uniformity and strong adhesion properties. This approach counteracted the risk of delamination under high load conditions during worst-case scenario testing and ensures their longevity when in use.
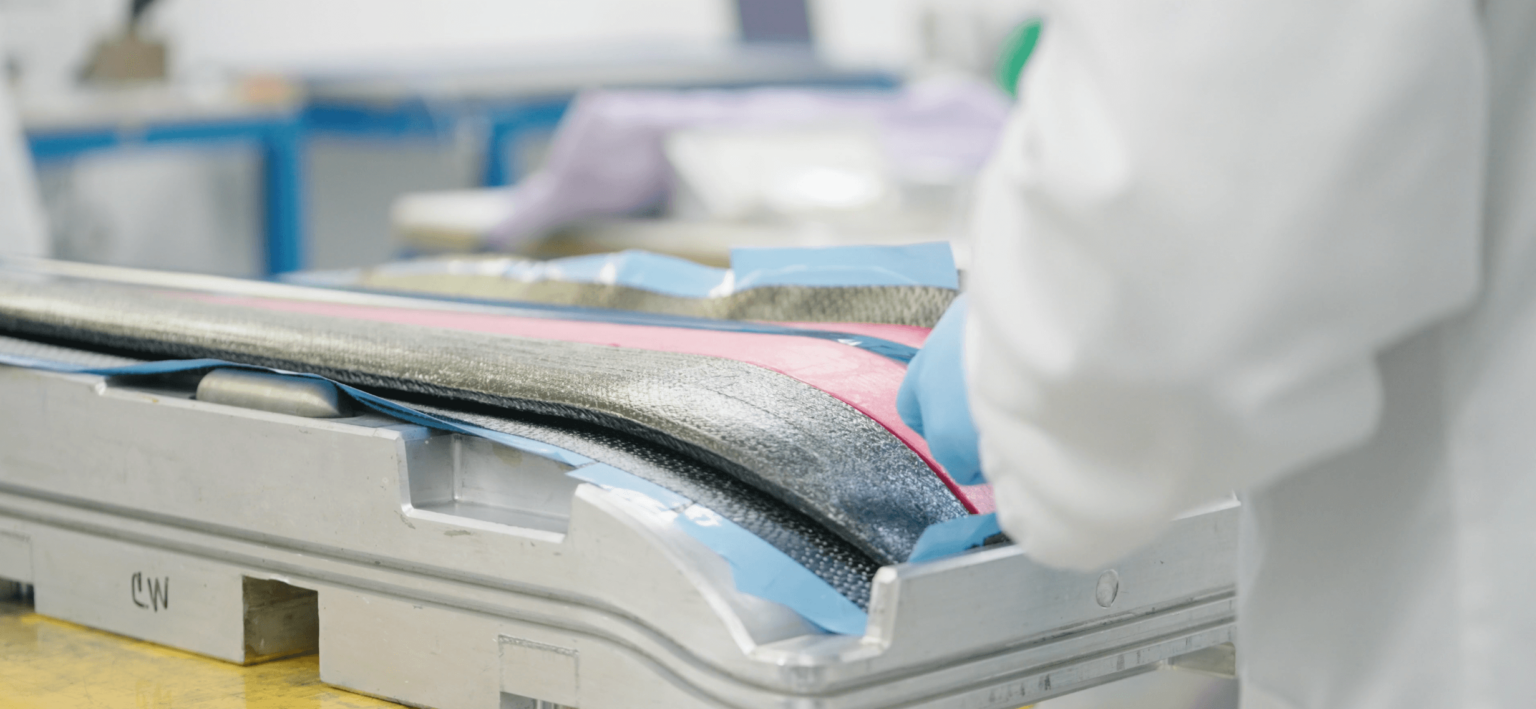
Results
Rockwood Aerospace’s compression moulding technique delivered propellor blades with 0% voiding between the skin, core, and spar materials, eliminating the need for secondary bonding. This resulted in increased fatigue performance, enhanced stiffness, and reduced weight compared to the Gen 1 version.
Vertical Aerospace’s VX4 eVTOL (electric vertical take-off and landing) aircraft, which is at the forefront of sustainable aviation, now uses Rockwood as their supplier of choice for forward blades. Rockwood has already delivered over 50 propellor blades to Vertical Aerospace, including the 20-blade set featured on the latest VX4 aircraft and continues to drive innovation in the aerospace industry in many other projects and challenges.