Processes
COMPRESSION MOULDING

Composite compression moulding produces cored and/or monolithic components in a one-shot moulding process. This method of manufacture uses aluminium tooling and heated platen presses, the pre-preg, foam cores, metallic inserts and integrated hardware is co-cured in a single shot process, thus eliminating the need for secondary bonding procedures in a lot of instances.
Components with undercut and side features can all be moulded using tooling with modular tooling inserts and side actions. The resultant parts have a moulded face on all surfaces and edges.
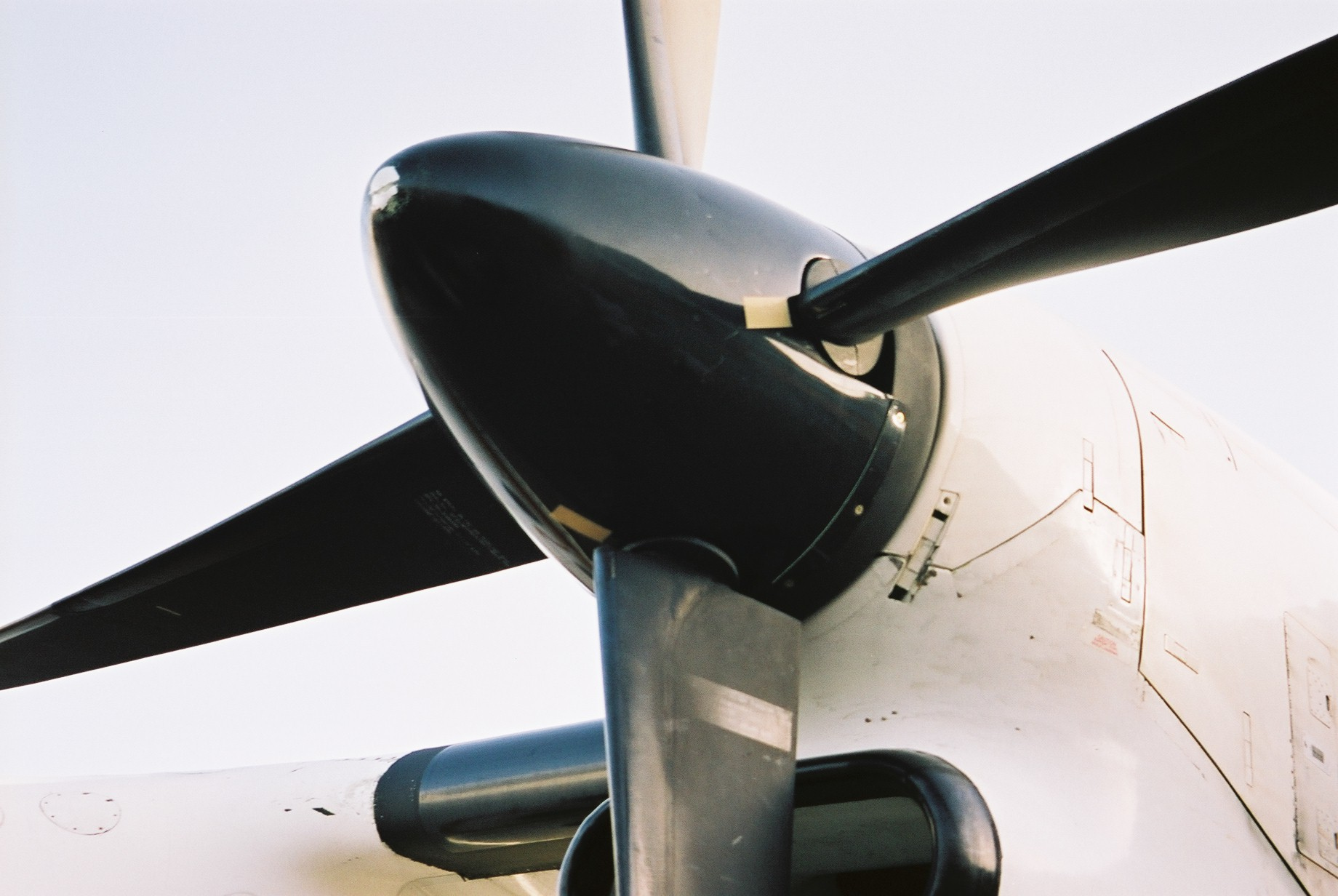
Composite compression moulding can also utilise a moulded core, in comparison to foam cores machined from a block, they reduce waste, speed up processing and are most often a more cost-effective approach to foam cored structures.
The benefits of compression moulding in aluminium tooling is the ability to use modular tooling – this is when you can mould a number of similar components from a single mould tool with the use of removeable and interchangeable inserts that change certain aspects of the part.
A further key benefit is the ability to combine compression moulding and bladder moulding into a single tool, allowing for component complexities that only this process can achieve, you can find out more about bladder moulding here.
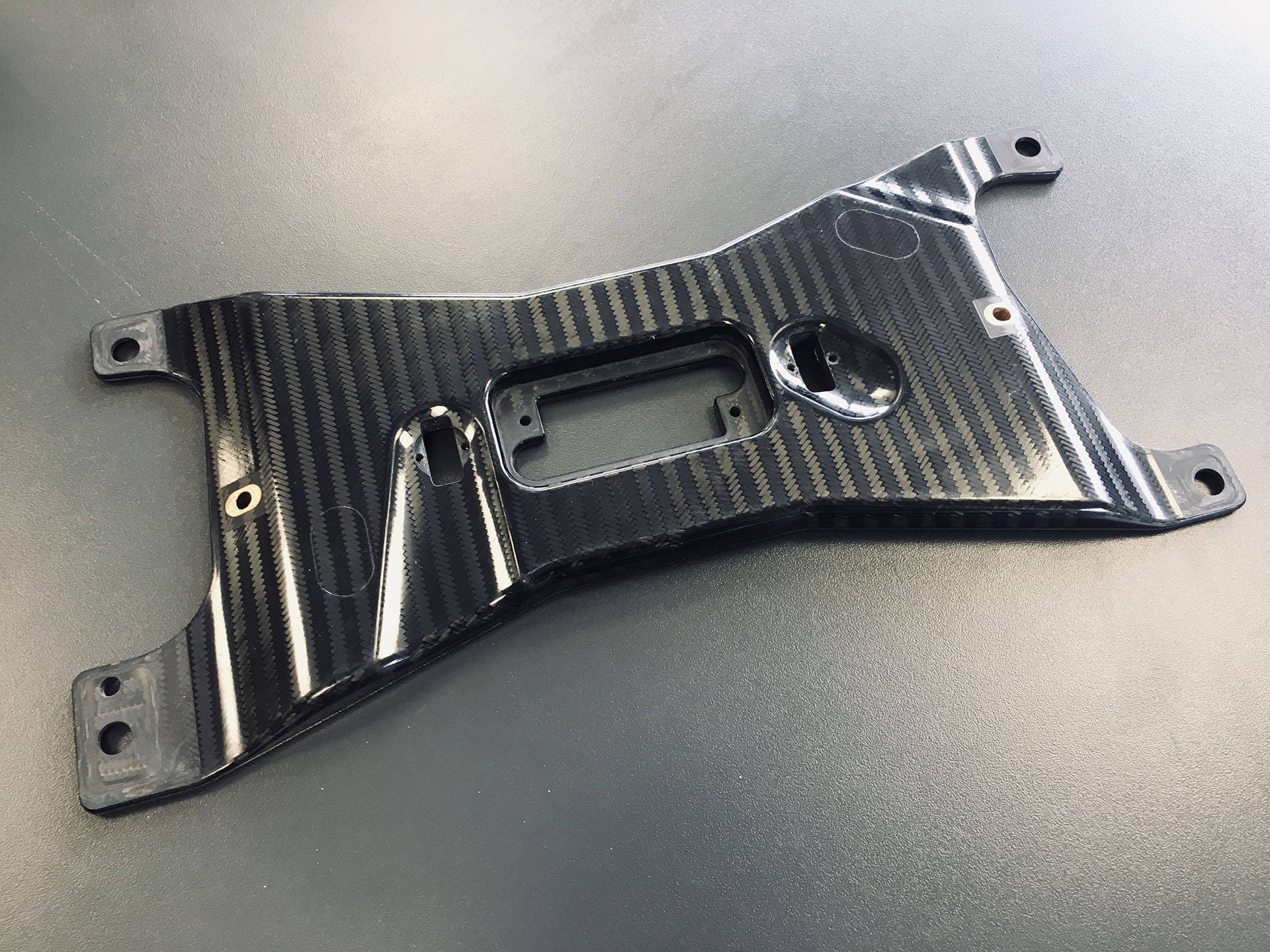
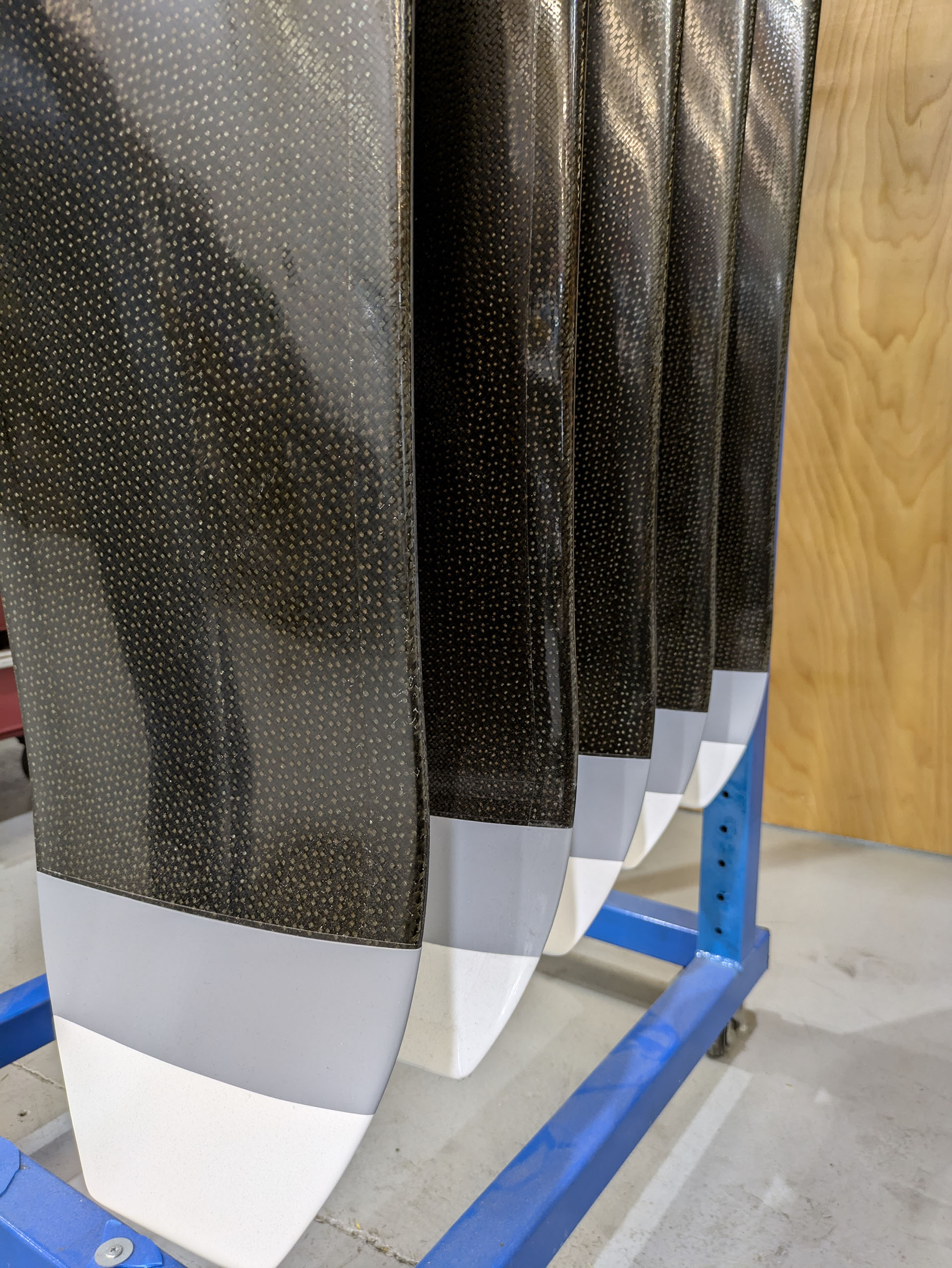